Von Holzspänen, über Papier, zur Dämmplatte.
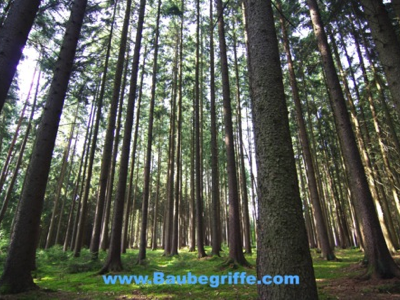
• Vor ca. 32 mio. Jahren: Menschenaffe Karl-Josef (Name geändert) erfindet vielleicht beim Versuch einen Zahnstocher zu schnitzen Holzspäne. Damit ihm kein anderer das Patent klaut, versteckte er die Späne unter seinem Schlafplatz. Schnell merkte er, dass es dort, wo die Späne liegen, Nachts nicht mehr so kalt war. Der Dämmstoff Holzwolle war erfunden!
• 105 n. Chr. Der chinesische Ackerbauminister Tsai-Lun erfindet ein Verfahren zur Papierherstellung, zu welchem er neben Seidenabfällen auch den Bast des Maulbeerbaumes verwendete, und schreibt diese nieder.
• 1100 – 1200 So langsam kommt Papier nach Europa. Das Suchen nach dem bestgeeignetsten heimischen Rohstoff beginnt.
• 1860: Die großindustrielle Papierherstellung aus Holzfasern in Deutschland beginnt im laufenden Jahrzehnt.
• 1918: Prof. Dr. Diels beschreibt erstmals ausführlich die Zelluloseproduktion aus Holz für die industrielle Herstellung von Papier in seinem Werk „Ersatzstoffe aus dem Pflanzenreich“ und erwähnt : „Die Gewinnung von Spinnfasern aus Holz der Nadelhölzer ist nach dem Verfahren von Mitscherlich gelungen.“
• 1932: Eine Papierfabrik in Cham (Schweiz) beginnt mit der industriellen Aufbereitung von Holzzellulose zu Hartfaserplatten. Die produzierten Platten kommen unter dem Namen Pavatex auf den Markt. Die Firma Gutex beginnt in Waldshut-Tiengen mit der Produktion der Holzfaserplatte „Fahrnit“.
• 1998 Die Firma Steico beginnt mit der Herstellung von Holzfaserdämmplatten in Feldkirchen.
• Heute: Alles, was außerhalb von dauerhaft feuchten Gebäudeteilen ist, kann mit Holzfaserprodukten gedämmt werden.
Nein, neu ist die Nutzung von Holzfasern zur Dämmung sicherlich nicht. Auch wenn es sehr wahrscheinlich nicht Karl-Josef war, der die ersten Holzspäne unter sein Mammutfell legte und Tsai-Lun mit der Erfindung der Papierherstellung auch nicht wirklich daran dachte, dass sein Verfahren der Grundstein für die heutige Produktion von Holzfaserdämmplatten ist. Dennoch ist klar, dass beide Ideen; feine Holzspäne schützen vor Kälte, Holzfasern kann man aufweichen und in Form bringen, der Beginn, der heute auf dem Markt vorhandenen Dämmprodukte aus Holz waren.
Für die Herstellung von Holzfaserdämmplatten in Europa werden Schwarten, Späne und Hackschnitzel (Verschnitt aus den Sägewerken) der Gemeinen Fichte (Picea abies) verwendet. Fichtenholz hat den Vorteil der hohen Verfügbarkeit und einer besonders gut geeigneten Faserqualität, welche den fertigen Dämmplatten im Verhältnis zur Rohdichte eine hohe Festigkeit verleiht. Aufgrund der vorhandenen Porosität ist Holz allgemein ein schlechter Wärmeleiter und eignet sich daher gut als Wärmedämmstoff im Bauwesen. Dieses, ohnehin schon sehr gute Wärmedämmvermögen wird durch das Zerfasern des Holzes und der somit erreichten Erhöhung der Porigkeit weiter verbessert, womit ein werksmäßig hergestellter, hoch wärmedämmender Plattenbaustoff produziert werden kann. Diese Zerfaserung kann im Nass- oder Trockenverfahren vollzogen werden, wobei nachfolgend das gängigere Nassverfahren beschrieben wird.
Die „Holzabfälle“ der Sägewerke, welche beim Antransport eine Holzfeuchte von ca. 50% haben, werden zunächst zu Hackschnitzeln verarbeitet und nach Entzug der Fremdpartikel über Rüttelsiebe und Elektromagnete (Metallbestandteile) unter Einwirkung von Wasserdampf im Dampfdruckzyklon aufgeweicht. Die anschließende thermomechanische Zerfaserung wird über ein Defibrationsverfahren vollzogen. Hierbei werden die eingeweichten Hackschnitzel zwischen profilierten Mahlscheiben aus Metall zerfasert. Je nach später hergestellter Produktvariante können die nach dem ersten Mahlen gewonnenen Fasern nochmals über einen Raffinator nachgemahlen werden.
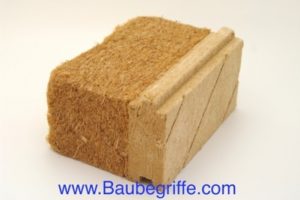
Durch diese Aufschlussprozesse wird die Faseroberfläche so weit aktiviert, dass beim späteren Trocknen der Holzfaserdämmstoffe die holzeigenen Bindekräfte (z. B. Hemizellulosen, Lignin u.s.w.) zusammen mit Wasser zur Abbindung gebracht werden. Eine Beigabe von zusätzlichen Bindemitteln ist in aller Regel nicht notwendig, wird jedoch bei manchen Produkten zur Erhöhung der Festigkeit oder des Wasserabweisungsverhaltens beigemengt. Hier kommen dann vor allem harz- und bitumenhaltige Bindemittel zum Einsatz.
Die Faserschlämme, welche aus bis zu 98% Wasser besteht, wird im nächsten Schritt in Bütten (Mischbütten) zwischengelagert und in einer Formstraße zu einem Faserkuchen gepresst. In der Formmaschine hat das Holz-/Wassergemisch noch etwa 42% Wasseranteil. Nach diesem mechanischen Auspressen, bei welchem ein Großteil des Wassergehaltes entnommen wurde, gelangt der Faserkuchen, nach einem Zuschnitt auf das gewünschte Längenmaß, in einen Trockenkanal (Etagentrockner). Im weiteren Produktionsverlauf werden die Holzfaserplatten bei einer Temperatur zwischen 160 und 220°C getrocknet und anschließend konfektioniert, d.h. auf Format geschnitten, profiliert oder für größere Dämmplattendicken mit einem i.d.R. wasserlöslichen Weißleim schichtverklebt.
Nach der Trocknung hat die entstandene Faserplatte noch einen Feuchtegehalt von ca. 7% und ist somit zur Verpackung und den Abtransport zum Handel bereit.
Die auf diese Art hergestellten Holzfaserdämmplatten enthalten folgende Inhaltsstoffe:
98 – 99 % Fichtenholzfasern
0,5 – 0,8 % Paraffin (gesättigte Kohlenwasserstoffe)
0,02 – 0,05 % Flocculant (Aufflockungsmittel div. Zusammensetzung)
< 1,6 % Polyvinylacetat aus allen Stoffen
Holzfaserdämmplatten werden zu meist bei Dämmarbeiten der Dachflächen eingesetzt, können jedoch auch wunderbar als Dämmstoff in oder auf Decken, für allgemeine Innendämmungen oder in einem verputzen Wärmedämm-Verbundsystem an der Fassade (oberhalb des Spritzwasserbereiches) eingesetzt werden. Letzteres wird zwar so langsam mehr und mehr bekannt aber dennoch, in Relation gesehen, viel zu selten angewendet. Nur schwer verständlich, erkennt man, dass bei Arbeiten mit Dämmplatten aus Holzfasern weit geringeren gesundheitlichen Belastung auftreten als bei synthetisch hergestellten Dämmplatten, die gerne mal hoch giftige Gase ausdünsten oder auch bei mineralischen Faserdämmprodukten, deren Bestandteile nicht selten hoch krebserregend sind.
Neben dem gesundheitlichen Aspekt ist aber auch die simple Verarbeitung im WDVS als Vorteil zu nennen. Wie alle bekannten Dämmplatten für verputze Dämmsysteme werden auch diese Platten auf den Untergrund geklebt und verdübelt, erhalten hiernach eine Armierungsspachtelung und abschließend einen Oberputz mit einem Egalisierungsanstrich. Mörtel, Armierungsgewebe und Dübelmaterial sowie alle anderen Zusatzprodukte sind vollkommen identisch mit denen einer Dämmung mit z. B. Polystyrol- oder Mineralwolledämmplatten. Einziges kleines Manko: Die Dämmwirkung ist nicht ganz so hoch wie bei den synthetischen Produkten, ergo man muss etwas mehr Dämmstärke einplanen. Aber auch dies dürfte für jemanden, der ein weitestgehend schadstofffreies Haus und somit ein wohngesundes Zuhause haben möchte, kein Problem darstellen.
Auszug aus dem Fachbuch: “Natürliche und pflanzliche Baustoffe” Gerhard Holzmann et al., Vieweg-Teubner Verlag